Real-time dust monitoring has really come into its own in the last few years. The ubiquity of real-time monitoring devices and the recent emergence of intelligent dust exposure control applications and platforms like GCG’s ‘Exposi’ system have taken monitoring and management of dust exposure to a new level. Hygienists and safety professionals now have the ability to make smarter, faster decisions around dust control management.
Real-time hardware devices capture data and with advanced software systems you can interpret, analyse and store data, and manage exposure controls in one place. As well as being able to identify harmful dust exposures faster, you can now test controls task by task in real-time, which is facilitating a shift in focus toward active dust control verification, management and optimisation to reduce risk and worker exposure to dust.
What is driving real-time monitoring?
While advancements in real-time technologies are impressive, it’s important to keep in focus the underlying driver for the push toward making real-time powered dust monitoring a priority.
The National Silicosis Prevention Strategy 2023-2028 Draft (Feb 23) and accompanying National Action Plan released by the Lung Foundation Australia noted a sharp rise in levels of Respirable Crystalline Silica RCS exposure, with approximately 600,000 Australian workers currently occupationally exposed to RCS. It also notes available data indicates the prevalence of silicosis is increasing in all states and territories and across several industries. The National Silicosis Prevention Strategy states:
“The number of Australians recently diagnosed with silicosis, particularly associated with engineered stone work, has caused government, health professionals, businesses, unions, and workers to call for safer workplaces to protect workers, reduce disability and stop premature deaths.
A comprehensive approach is needed that includes failsafe preventive measures, strong legislation and regulation that is consistently enforced, coordinated surveillance and monitoring, expanded air monitoring programs and improved health screening methods.”
With heightened public awareness of the threat of silicosis, increasing regulatory pressure from state and federal government authorities, and increasing awareness of workers at risk of exposure, forward-looking companies across mining, construction, manufacturing and other dust-generating related industries are no longer looking at dust control management through a compliance lens alone.
Real-time monitoring technologies allow for improvements to worker risk reduction going beyond just meeting compliance requirements to ensure workers are provided the best protection against exposure to dust.
How does integrated real-time dust monitoring and control management work?
Real-time monitoring uses a hardware device to capture data, which feeds into a compatible hygiene software or application allowing you to interpret and analyse the data in real-time, so you can quickly address your dust exposure events.
The expediency of real-time data allows safety professionals and operations teams to quickly test, compare and validate exposure controls to address exposure events and mitigate risk of future events by designing appropriate controls for a particular scenario, environment or task.
With real-time data, once you’ve found a control that works, you can move to ongoing monitoring to ensure your controls continue to work as expected. Over time you can build a bank of exposure control intelligence that allows you to share insights with your team and throughout your business.
Real-time monitoring underpins a real-time data-driven approach for better controls management and smarter, faster control decisions to reduce worker exposure to dust.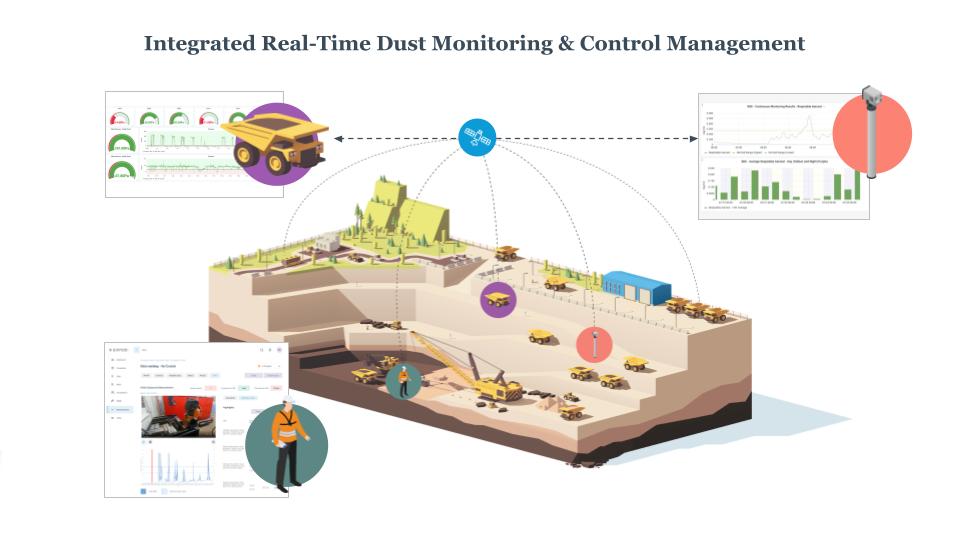
How is real-time data captured?
Gathering real-time dust data on a worksite happens in three main ways:
- On-person task monitoring, often paired with video,
- Workplace area monitors, and
- Positive pressure cabin sensors for vehicles and other stationary cabin environments on a worksite.
Personal real-time dust monitoring
Real-time personal monitoring or personal task monitoring involves a worker, or workers, wearing a dust sensor to measure the dust in their breathing zone. The wearable sensor captures real-time monitoring data while your team go about their daily tasks. A log of what they’re breathing is recorded every second they’re working. This data is uploaded to a real-time app (Like GCG’s Exposi), letting you immediately detect where dust exposures occurred.
Personal real-time dust monitoring is often combined with video footage captured on a camera also worn by the worker, which is synced with the dust measuring data allowing you to see exactly what the worker was doing when the exposure occurred.
With this level of instant visibility, you can efficiently test task-specific controls to improve worker safety. You can also validate existing controls and potentially reduce unnecessary costs on controls you may not need.Area (workplace) real-time dust monitoring
Remote area monitoring allows you to monitor for changes in levels of dust particles site-wide or at a specific work location, remotely and around the clock. Remote area monitoring is usually carried out for two main purposes:
- To provide feedback on the effectiveness of your existing or new dust control measures and/or
- Report on changes in the ambient conditions that workers may be exposed to
The monitor unit sends real-time respirable dust data to a web platform, allowing for remote real-time analysis and reporting to site stakeholders via dashboards.
If abnormal dust levels are detected outside the predetermined normal range for a work area, an alert is triggered and sent via the app, allowing you to respond immediately and take appropriate action.Real-time cabin pressure monitoring
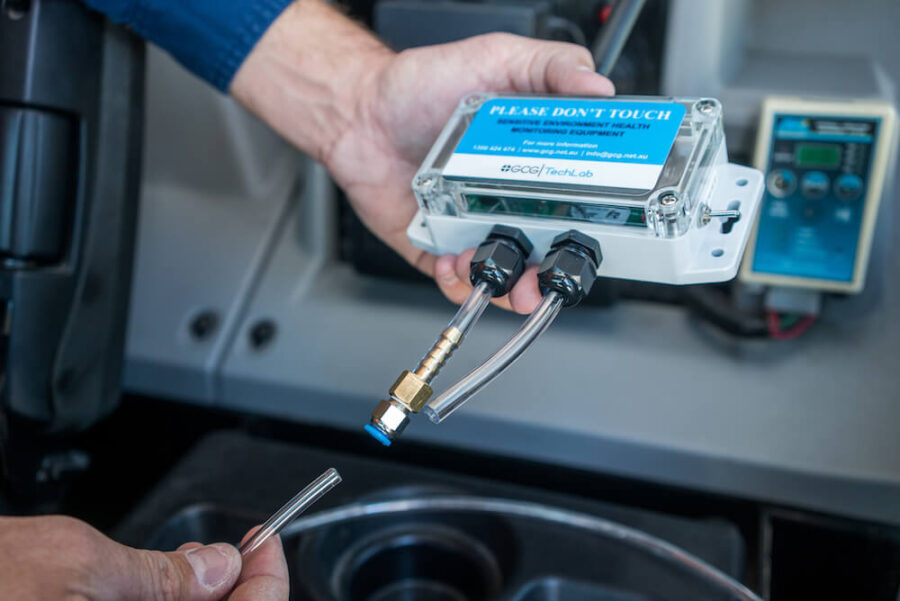
Vehicle cabins are a critical control to isolate operators from harmful airborne contaminants in the outside environment including crystalline silica and respirable dust.
Cabins require regular testing to ensure they’re working effectively to protect workers. This traditionally requires a vehicle to be parked up for maintenance and a person deployed to conduct the testing. Now, cabin pressure can be measured remotely in real-time while the vehicle is operating, allowing you to measure the effectiveness of the control.
Using a sensor inside the cabin to measure differential pressure (inside versus outside the cabin), the effectiveness of the cabin in controlling dust from entering can be determined. The ‘always on’ monitoring means you know right away when the risk to worker health has increased and maintenance is required to protect workers.
With traditional testing, risks to worker health may not be detected until scheduled testing is carried out, potentially exacerbating worker harm.
As well as reducing the need for traditional scheduled cabin testing,real-time monitoring also provides insights into the performance of the cabin over time. It helps to identify maintenance items in advance for preventative maintenance, limiting unplanned maintenance and helping to reduce time loss.
Final thoughts
While Australian enterprise is at the forefront of the evolution and sophistication of real-time dust monitoring and control management technology development, legislative requirements and compliance regulations have not kept up with advancements in dust monitoring available to reduce worker exposure to dust. However, international think tanks and research organisations recognise the inevitability of a real-time monitoring led future.
In the meantime, a modern approach to occupational hygiene management involving a combination of traditional compliance-led monitoring with real-time techniques delivers the best way to accelerate dust exposure reduction.
